2024.03.18
お知らせ協働ロボットは産業用ロボットと異なり特別教育が不要なため、導入は簡単だと思っている事業主もいるのではないでしょうか。協働ロボットは産業用ロボットよりも危険性が少ないロボットです。
しかし、協働ロボットの設置場所や従業員の配置に問題があると従業員に危険が及びます。協働ロボットの導入前には、安全規格に基づいた製造現場のリスクアセスメントが必要です。
この記事では、協働ロボットのリスクアセスメントの参考となる安全規格や具体的な安全対策について解説します。協働ロボットの安全規格に基づき、リスクマネジメントを行えば、従業員とロボットの接触事故を未然に防げるでしょう。
協働ロボットの安全規格
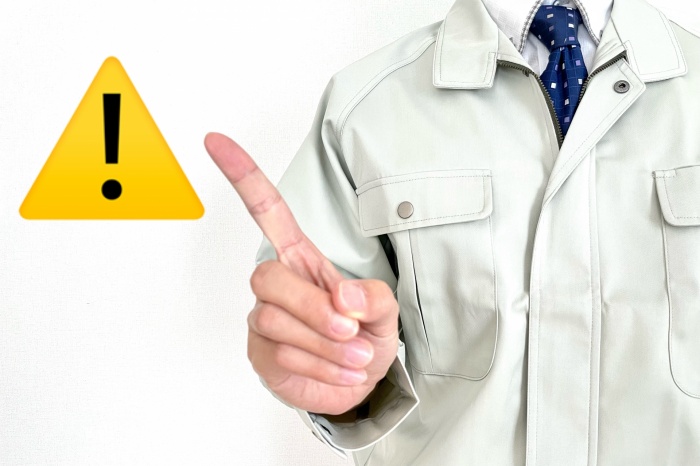
協働ロボットを安全に操作・点検するために考慮すべき安全規格は次の通りです。
規格 | 概要 | 対象 |
ISO 10218-1 | ロボットの設計上の安全や製造上の安全を保証するための要求事項 | 協働ロボットを含める産業ロボット |
ISO 10218-2 | ロボットの設計上の安全や製造上の安全を保証するための要求事項 | システムインテグレーター(事業所にロボット導入するのをサポートする専門業者) |
ISO/TS 15066 | ISO10218-1を補完するために制定された協働ロボットの安全要求事項 | 協働ロボット |
協働ロボットを導入するときには、これら3つの安全規格を熟知しておきましょう。
協働ロボットのリスクアセスメントとは?
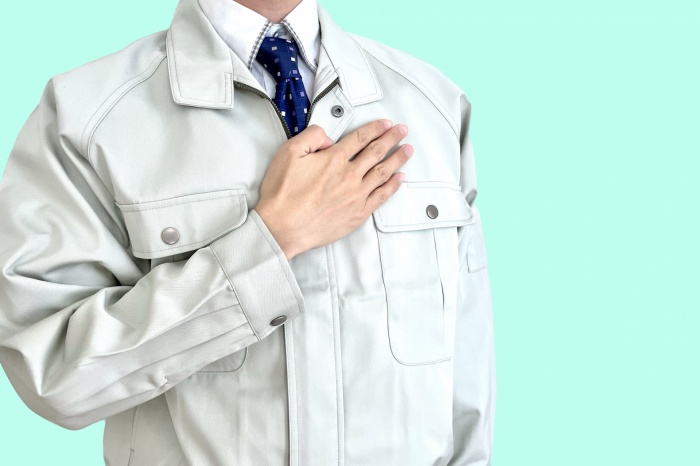
協働ロボットを導入するには、リスクアセスメントが必要になります。リスクアセスメントとは、協働ロボットを安全に稼働・点検するため、事前に発生しうる事故の被害や頻度を予測し、優先順位をつけてリスクの除去や低減などの安全対策をおこなうことです。
協働ロボットは、産業用ロボットよりも安全性が高いと言われていますが、従業員と同じ生産ラインで作業をするため、思わぬ事故が発生する可能性があります。
従業員の安全性を担保するため、リスクアセスメントの実施は労働安全衛生法において、努力義務という位置づけになっています。
協働ロボットのリスクアセスメントの手順
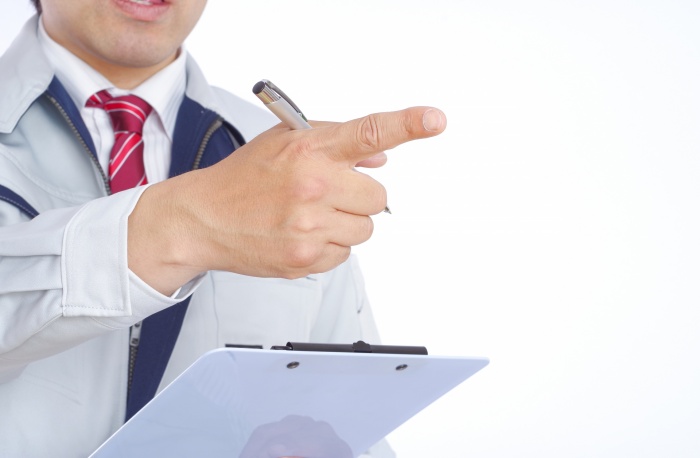
協働ロボットのリスクアセスメントは基本安全規格「ISO 12100」に基づき実施しましょう。基本安全規格「ISO 12100」とは、協働ロボットを含む機械安全を製品に適用するための規格です。
人に対する危害のリスクを考慮した機械設計をするための、リスクアセスメントの具体的な方法が制定されています。基本安全規格「ISO 12100」に基づいた協働ロボットのリスクアセスメントの具体的な手順を確認していきましょう。
動作制限の決定
協働ロボットを導入するときには、まず協働ロボットや周辺機器を使用するときの動作範囲や設置場所、動作速度などを決めていきましょう。協働ロボットを制御しないと、稼働したときにロボットが暴走し、従業員に危害を加えてしまう可能性があります。
協働ロボット導入前に決定しなければならない具体的な項目は次の通りです。
・設置場所の制限
・動作範囲の制限
・運転寿命
・各部品の寿命
・メンテナンスの頻度
協働ロボットの設置場所や動作範囲を決定するときには、従業員とロボットをどの位置に配置するか、レイアウトを検討する必要があります。協働ロボットは従業員とロボットが同じスペースで作業をするため、事故が発生しないよう、双方に十分なスペースを設けましょう。
ロボット周辺にある危険源の特定
協働ロボットの動作制限を決定したら、ロボット周辺にある危険源を特定しましょう。作業中の事故を防ぎ、従業員と協働ロボットが安全に生産活動をするには、事前に危険源を特定し、回避する方法を検討する必要があるからです。
基本安全規格「ISO 12100」には、協働ロボットを含む機械類の危険源一覧が掲載されています。
・機械の接触や巻き込み
・感電
・熱源による火傷
・低温による凍傷
・騒音による耳鳴り・ストレス
・振動による神経障害
・紫外線や赤外線照射による人体への障害
・化学物質による呼吸困難や腐食
上記を参考にしながら自社に協働ロボットを導入したときに発生しうる危険源を特定し、洗い出しましょう。
リスクレベルの見積り
協働ロボットや周辺機器の危険源を特定したら、それぞれの危険源のリスクレベルを見積りましょう。リスクレベルの見積りに必要となる要素は次の3つです。
・事故発生時の重篤度(被害の大きさ)
・危険の発生確率
・危険の発生頻度
これら3つの要素を数値化し、合計した数値が協働ロボットのリスクレベルになります。重篤度や発生確率、発生頻度の点数は、厚生労働省が公表している「リスクアセスメント評価基準(例)」を参考にしましょう。
たとえば、「協働ロボットの稼働時に接触事故の可能性」があったとします。このとき重篤度が「重症(6)」・発生確率「可能性が高い(4)」・頻度「時々(2)」と見積ると、リスクレベルは「12」になります。
リスクの評価
危険源に対し、すべてのリスクの見積が終わったら、リスクレベルの値に応じて評価を実施します。リスクの評価は、厚生労働省が公表している「リスクアセスメント評価基準(例)」を参考にします。
たとえば、先ほどの「協働ロボットの稼働時に接触事故の可能性」のリスクレベルは12です。リスクの優先度は「リスクⅣ」になるため、早急な安全対策が必要な危険源と言えるでしょう。
リスクの除去・低減するための安全対策
リスク評価の結果、リスクレベルが高い危険源については、リスクの除去・低減するための安全対策が必要になります。リスク低減が必要な危険源に対しては、3ステップメソッドによる保護対策が必要です。
ステップ1:本質的安全設計方策
ステップ2:安全防護および追加保護方策
ステップ3:使用上の情報
ステップ1・2によってリスクが低減できない場合は、操作マニュアルの整備やラベルによる警告などで従業員に注意喚起を促しましょう。
残留リスクの確認・処置の検討
安全対策により、残留リスクのレベルが小さくなった場合は、リスクなしと設定することが可能です。ただ安全対策を講じても、リスクが残る場合は、危険源が存在していることを従業員に周知・教育するとともに、マニュアルやラベルなどで注意喚起する必要があります。
協働ロボットのリスクアセスメントの安全対策事例
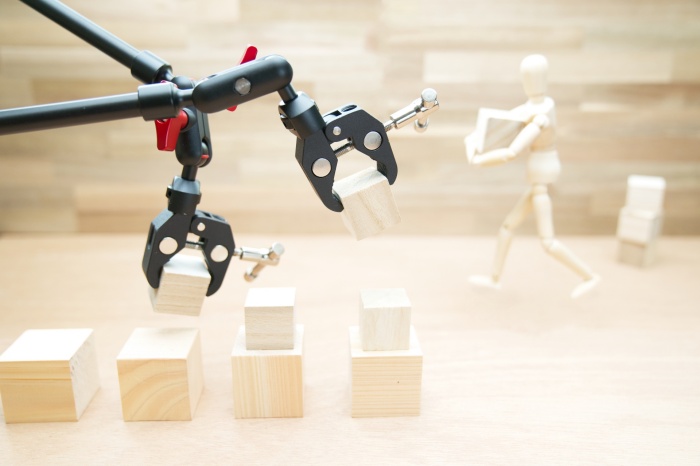
協働ロボットのリスクアセスメントで、リスクの高い危険源を特定した場合、従業員への呼びかけやマニュアルの変更だけでは事故を防げないこともあります。ここからは、協働ロボット稼働時の事故を未然に防ぐための、物理的な安全対策事例をご紹介します。
エリアセンサの設置
従業員の侵入に対して、協働ロボットが検知し停止するようエリアセンサの設置を検討しましょう。協働ロボットの作業中に従業員が意図せず侵入してしまうと、接触事故が発生してしまうかもしれないからです。
また、エリアセンサを設置したとしても、人の侵入を検知してからロボットが停止するまでに時間を要します。エリアセンサを設置するときには、検知からロボット停止に必要な反応時間とその速度を考慮した設定を忘れないようにしましょう。
安全速度制限
協働ロボットの作業範囲に従業員がいる場合は、安全速度制限をかけましょう。万が一、接触してしまったときに従業員の被害を最小限に抑える必要があるからです。
協働ロボットの安全速度制限は、安全規格によりTCP(ツール・センター・ポイント)速度が、250mm/sを超えてはならないと定められています。
必要に応じて安全柵の設置
協働ロボットは、条件を満たした状態であれば、安全柵なしで従業員と同じ作業スペースで稼働が可能です。しかしながら、条件が満たせない場合は、安全柵を設置する必要があります。
ICS SAKABEは現場従業員が設置・プログラムできる移動式協働ロボットを提供
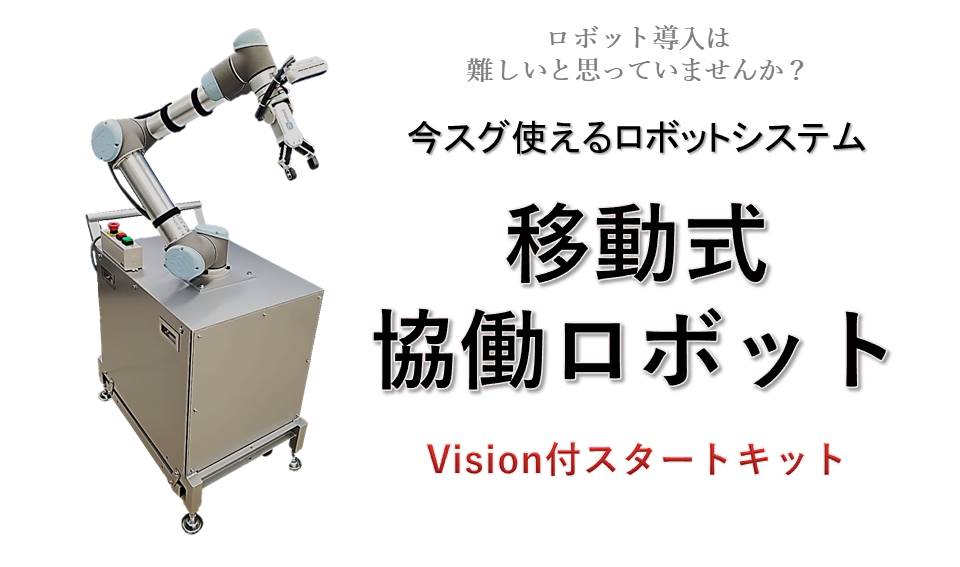
協働ロボット導入時に、リスクマネジメントを実施し、リスクを除去・低減させるための対策を講じたとしても、「実際に導入したら稼働時に扱いづらかった」ということもあるかもしれません。
九州・福岡にあり、複数の産業用ロボットをつなぎ合わせて設定する技術を保有するICS SAKABEでは、移動式協働ロボットを提供しています。
移動式協働ロボットのおすすめポイントは、「作業内容の変更が簡単にできる」「作業場所の変更が簡単にできる」ことです。初めて協働ロボットを導入する事業者がすぐに活用できるよう、協働ロボット・専用移動担架台・導入サポート・セミナーがセットとなっています。
現場作業員が移動・設置・プログラムできるので、自社の生産ラインに合わせた設定が可能です。「協働ロボットを1台だけ導入してみたい」「自社で簡単に設定変更できるロボットが欲しい」。このように考えている事業者様は、ぜひ公式サイトから問い合わせしてみてください。
まとめ
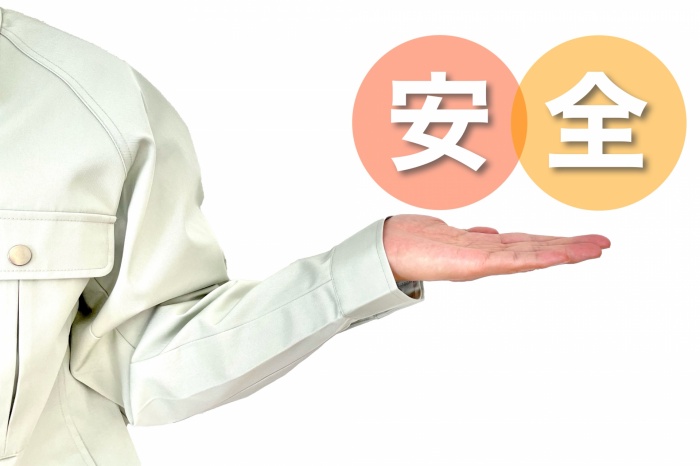
協働ロボットを導入するときに、特別教育の受講は不要です。しかし協働ロボットが安全に稼働できるか、事前に製造現場をチェックするリスクアセスメントの実施が必要になります。
リスクアセスメントは、ISOの安全規格の内容を参考に実施します。しかしながら、リスクアセスメントでリスクを特定し、安全対策を講じてもチェック漏れなどにより、想定外の事故が発生することもあります。
事故被害を最小限に防ぐためにも、センサや速度制限機能追加を行いロボットと作業員が安全に作業できる環境づくりが大事です。